Why Bandsaw Blades Twist
Twisting is a frequent problem bandsaw users run into, and it can negatively affect cut precision and increase wear on your equipment. The issue typically results from poor blade storage, incorrect installation, or using an unsuitable blade for the material. A blade that doesn’t sit flat on the wheels will track unevenly, resulting in poor-quality cuts. Addressing the problem early helps maintain smooth cutting and extends blade life.
Signs You May Be Dealing with a Twisted Blade
-
High-pitched or irregular sounds during cuts
-
Blade appears to pull to one side
-
Teeth are not aligned square with the material
-
Inconsistent or curved cutting lines
-
Blade rubs against the guide blocks or housing
Steps to Straighten a Twisted Blade
Begin by safely removing the blade and laying it on a flat surface. Examine it for any visible bends or twists. If needed, gently adjust it back to a flat profile. When reinstalling, make sure the blade is properly seated on both wheels and that tracking is set correctly. Avoid tightening the blade beyond the necessary tension, as this can worsen any twist or create new alignment problems.
How to Store Blades the Right Way
Poor storage habits often lead to blade damage. Always coil bandsaw blades neatly and store them in a dry, stable place away from heat or pressure. Avoid tight kinks when uncoiling, and always handle blades carefully using gloves to maintain control and avoid injuries.
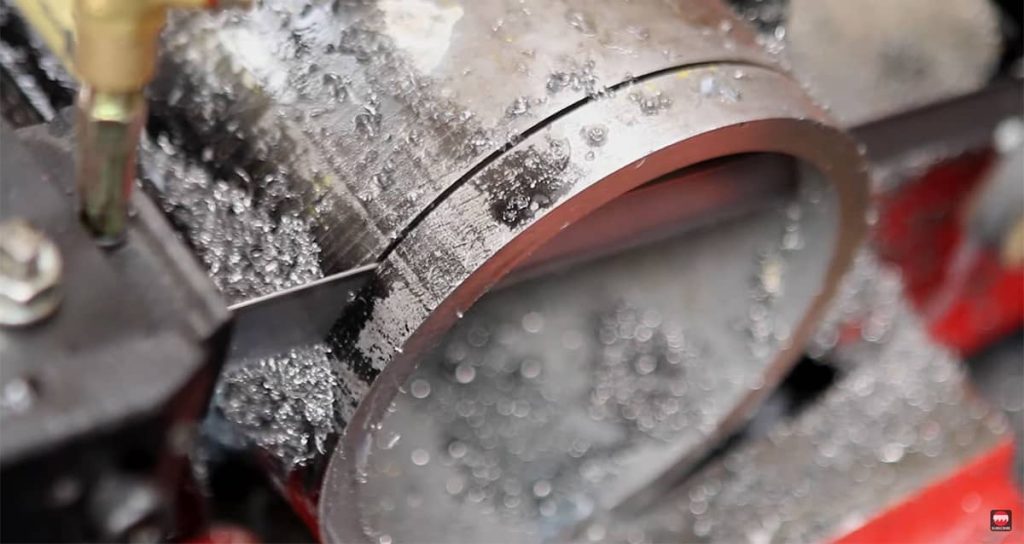
Tooth Pitch Recommendations by Material
Material Type | Suggested Pitch (TPI) |
---|---|
2″ x 2″ Angle Iron (3/8″ wall) | 4-6 or 3-4 |
Thin-Wall Tubing | 5-7 or 8-11 |
4″ x 4″ Box Tube (3/8″ wall) | 4-6 |
4″ Solid Round Stock | 3-4 |
8″ Solid Round Stock | 2-3 |
Choosing the right tooth pitch helps reduce pressure on individual teeth and minimizes vibration. Use fewer teeth for larger, tougher stock and finer pitch for thin-walled material.
Selecting the Right Blade for Your Material
A blade that’s the wrong size or type can lead to twisting, premature dulling, and poor cut quality. Always choose a blade that suits your application and is compatible with your machine. Blade width, thickness, and tooth shape should be matched carefully for reliable, consistent results.
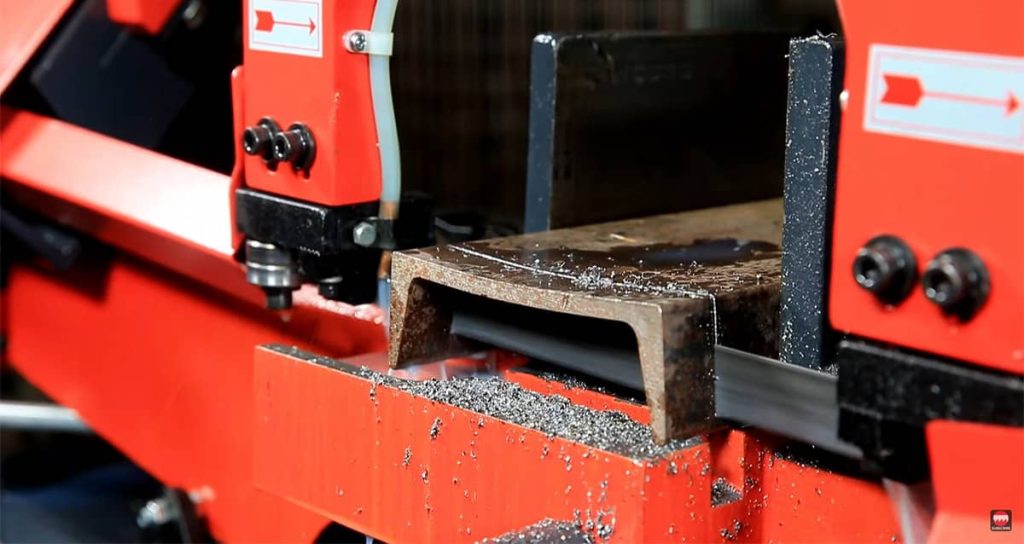
Best Practices to Minimize Blade Twist
-
Handle blades gently when coiling or uncoiling
-
Set tension to recommended levels only
-
Keep guides aligned and clean
-
Match pitch to the size and hardness of the material
-
Release blade tension when storing the tool
When It’s Time to Replace Your Blade
If your blade is showing signs of wear such as cracking, bent teeth, or repeated twist issues—it’s best to replace it. Continuing to use a worn or damaged blade can affect your machine’s performance and lead to further complications.
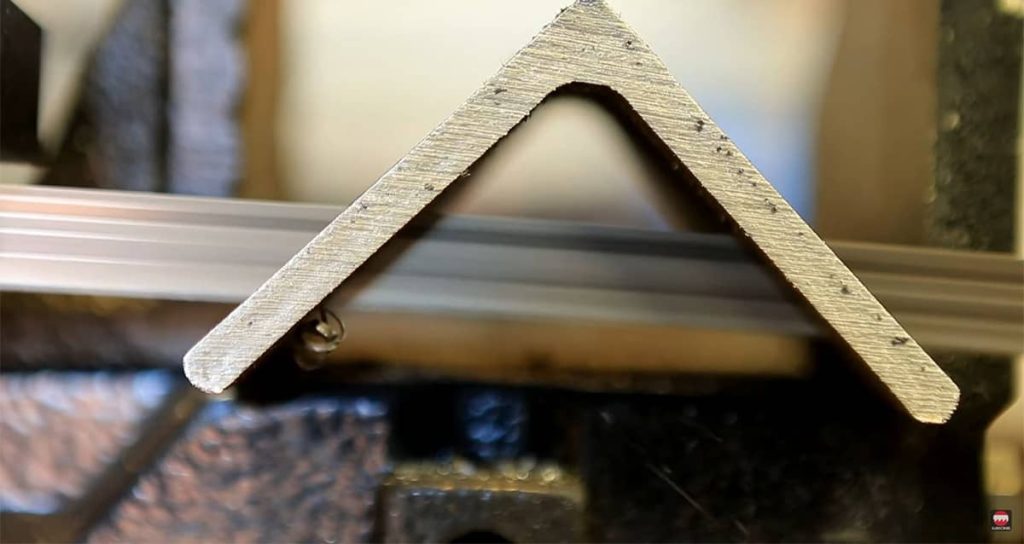
Blade Storage Tips That Make a Difference
-
Hang coiled blades neatly to retain their shape
-
Keep blades off the floor and away from clutter
-
Store them in dry areas to avoid rust
-
Mark used blades to monitor usage and wear
Need Help Finding the Right Blade?
For professional advice on blade selection, pitch matching, and setup, visit Sawblade.com. You’ll find helpful resources, including product breakdowns, how-to videos, and guidance based on the material you’re cutting. Whether you work with tubing, bar stock, or structural sections, they have a solution for you.
Not Sure What Size Blade Your Bandsaw Needs?
Choosing a blade with the correct length and width is essential for accuracy and safety. Visit our article “How to Determine the Correct Bandsaw Blade Size for Your Machine” to learn easy methods for measuring your saw and selecting a blade that fits properly. A well-sized blade prevents tracking issues and helps you get consistent results.
Blade twists can be avoided with a few simple habits—from careful handling and correct pitch selection to proper storage. Pay attention to early warning signs, and don’t overlook the importance of matching your blade to both the material and the machine. A little care upfront keeps your bandsaw cutting smoothly, safely, and efficiently.