Efficiently Sawing Inconel with Industrial Band Saws
An industrial band saw effortlessly cutting Inconel alloy, showcasing precise blade control, steady coolant distribution, and consistent cutting speed essential for effectively processing this demanding alloy.
Why is Inconel Difficult to Machine?
Inconel alloys are prized for their high nickel content, delivering outstanding corrosion resistance and durability. However, the alloy’s notable Rockwell hardness significantly complicates cutting operations. Extensively used in aerospace, energy, and heavy industry sectors, Inconel requires specialized cutting methods for productive machining. Implementing appropriate techniques ensures efficient cutting, prolongs tool life, and consistently delivers high-quality outcomes.
Band saws are an ideal choice for cutting Inconel due to their accuracy, adaptability, and controlled cutting capabilities. Selecting the correct blade and following proven best practices is vital for any operator frequently working with this challenging material.
Recommended Practices for Cutting Inconel:
To successfully handle Inconel alloy cutting, consider these essential practices:
-
Choose an Optimal Blade: Carbide blades such as the Q1002 Triple Chip Carbide Blade featuring a 2-3 tooth pitch are recommended. This blade reliably manages 7-inch diameter by 1.5-inch thick-walled materials, typically finishing cuts in 20 to 25 minutes.
-
Blade Speed Management: Operate blades at around 70 surface feet per minute (SFPM) to reduce heat, preserve blade sharpness, and ensure cutting accuracy.
-
Maintain Ideal Feed Rates: Target a steady cutting progression between 0.5 to 1 square inch per minute to minimize heat buildup and maintain cutting efficiency.
-
Proper Coolant Application: Regularly applying a quality cutting fluid helps dissipate heat, reduce friction, and prolong blade life.
Importance of Correct Blade Selection
Proper blade choice significantly impacts cutting effectiveness. Carbide-tipped blades such as the Q1002 Triple Chip Carbide are engineered specifically for hard-to-cut alloys like Inconel, offering excellent durability and shorter cutting cycles. These blades maintain a sharp cutting edge, ensuring cleaner finishes and extended operational life.
Recommended Bandsaw Speeds and Feeds for Inconel
Optimal cutting performance is achieved through proper bandsaw configuration. Cutting Inconel at approximately 70 SFPM with a carbide blade delivers precise results and minimizes blade wear. Consistent, controlled feed rates protect the blade and reduce downtime, maximizing production efficiency.
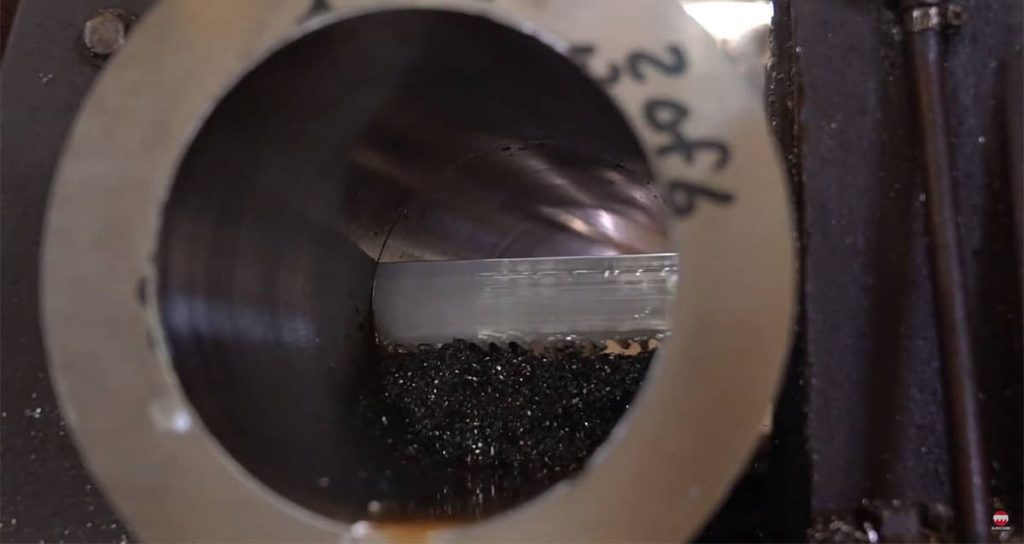
Ideal Band Saw Blade and Operating Parameters for Inconel:
Parameter | Recommended Specifications |
---|---|
Blade Type | Q1002 Triple Chip Carbide |
Blade Pitch | 2-3 pitch (ideal for 7” diameter x 1.5” wall materials) |
Blade Speed | Around 70 surface feet per minute (SFPM) |
Feed Rate | Between 0.5 to 1 square inch per minute |
Coolant | Consistent use of high-quality cutting fluid |
Blade Tension | Adjusted to blade manufacturer’s recommendations |
Minimize Downtime and Enhance Productivity
Implementing recommended blades and operating parameters significantly reduces downtime, boosting productivity. Regular blade inspections, timely replacement, and effective coolant application facilitate continuous, uninterrupted operation, essential for demanding Inconel cutting tasks.
Key Maintenance Steps When Working with Inconel:
-
Regularly inspect blades for wear and promptly replace when necessary.
-
Frequently verify blade tension and alignment.
-
Continuously apply coolant throughout cutting operations.
-
Keep the cutting area clear from metal shavings to optimize blade performance.
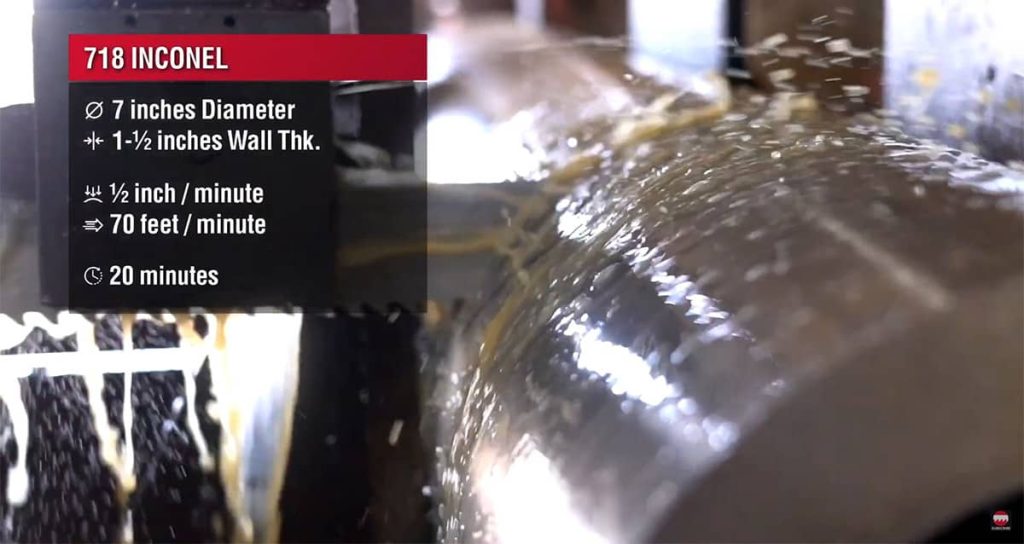
Reliable Precision for High-Demand Applications
Inconel’s unique attributes require precise cutting capabilities. Band saws equipped with specialized carbide blades deliver reliable accuracy crucial in aerospace, energy, and industrial applications. Proper blade selection, controlled speed settings, and regular maintenance guarantee predictable results and superior finished products.
Typical Inconel 718 Applications Include:
-
Aerospace engine and turbine components
-
Petroleum industry equipment
-
Structural parts for high-temperature environments
-
Offered in tubing, extrusions, solid stock, and structural forms
Immediate Benefits to Your Inconel Cutting Operations
Incorporating these best-practice techniques immediately enhances your cutting results. Choosing the correct blades, managing blade speeds effectively, and performing regular maintenance significantly boosts cutting quality and production efficiency, contributing positively to your operational success.
Quick Overview of Inconel Cutting Benefits:
-
Extended blade lifespan with fewer replacements
-
Improved accuracy and surface finish
-
Increased cutting efficiency and production rates
-
Reduced operational downtime due to proactive maintenance
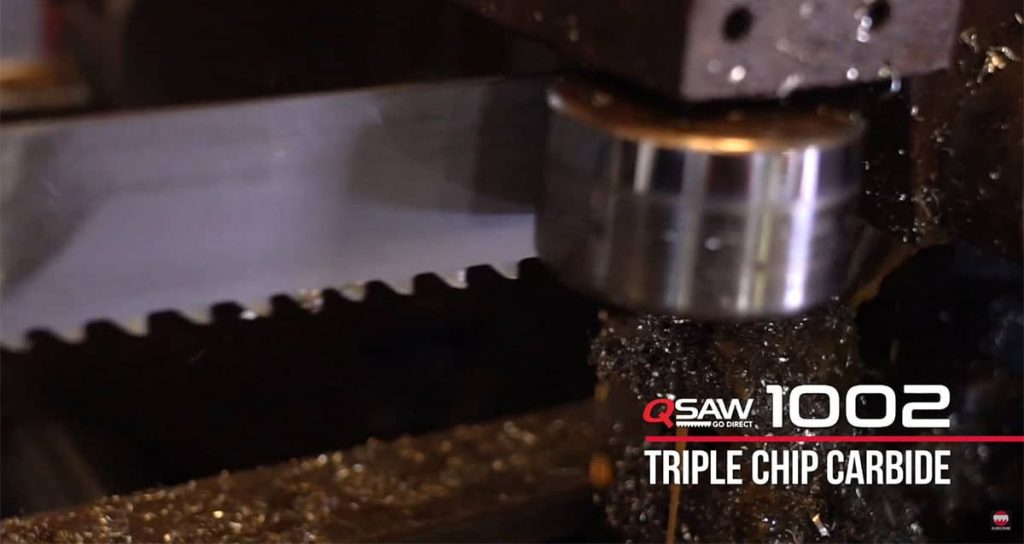
Further Boost Bandsaw Performance with the Q701 M71 Blade
To further increase your bandsaw efficiency, explore our related article, “Performance and Accuracy Combined: The Q701 M71 Blade Difference.” Discover how upgrading to the Q701 M71 blade improves precision, durability, and productivity, particularly with challenging materials like Inconel.
Discover the Advantages of the Carolina HD10 Horizontal Bandsaw
Interested in exploring durable and versatile cutting equipment for your workshop? Don’t miss our detailed article, “Key Features and Benefits of the Carolina HD10 Horizontal Bandsaw.“ Learn how this reliable bandsaw offers robust performance, ease-of-use, and consistent precision, making it ideal for various industrial cutting tasks and enhancing overall operational efficiency.
Protect Your Equipment for Lasting Results
Adhering to these best practices for cutting Inconel ensures maximum blade life, minimizes equipment wear, and consistently delivers superior quality cuts. Regular maintenance, although straightforward, yields substantial improvements, maintaining the effectiveness and high standards of your metalworking operations.